Pumped superconducting electromagnet
From NMR Wiki
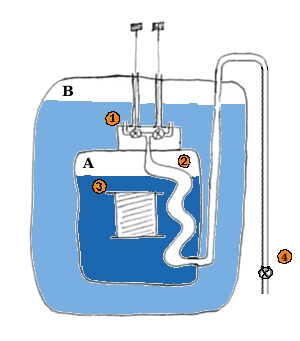
A) 2.18K He chamber
B) 4.2K He chamber
1) Needle valve block (More then one needle valve can be used for redundancy) set flow of 4K He into the refrigerator loop
2) Refrigerator loop where 4.2K He expands and cools to 2.18K
3) Magnet coil
4) Ball valve - isolates pumping system from the magnet
The coil of pumped superconducting magnets is cooled to ~2.2K (while "conventional" high field NMR magnets are cooled to 4.2K). Lower operating temperature allows the coil to sustain higher current densities and thus produce stronger magnetic field.
Lower coil temperature is achieved by actively pumping He from the coil chamber, therefrom comes the name "pumped magnets". The purpose of the pumped manget systems is to provide the extreme magnetic field which cannot be achieved with the current superconducting wire and joint technologies at 4.2 K
At this time commercial non-pumped magnets can produce field strength corresponding to ~800MHz proton Larmor frequency, while whith the pumped magnets fields up to 950MHz are accessible.
Evaporative cooling greatly increases helium consumption as the pumping process actively removes the helium from the upper bath. In most magnets between 500 and 800 MHz today, helium passively evaporates from the cryostat and must be replaced every 6-18 weeks. An actively pumped magnet would consume several times more helium.
Refrigeration system of pumped magnets
This part based on AMMRL discussion and is applicable to pumped magnet systems manufactured by Oxford Instruments. Thanks a lot to all contributors, especially Geoff Armstrong and Janusz Koscielniak.
Magnet has two chambers (A and B, see schematic figure)
The lower chamber (A) contains the magnet coil (3) immersed in the liquid He at around 2.18K, while the upper chamber (B) contains 4.2K He. The Helium in the lower tank is trapped permanently.
The system for cooling the lower chamber starts at the block with needle valves (NV's, 1) located at the bottom of the upper chamber. More then one NV might be installed for redundancy.
The NVs regulate the inflow of liquid He from the outer 4.2K chamber. The metered flow of He enters the piece of tubing called refrigeration loop (2) where He expands into the vacuum created by a rotary vacuum pump and rapidly cools.
Finally the vacuum pump is connected to the refrigeration loop via long large diameter corrugated tube. A large cross-section ball valve (4) isolates magnet from the pumping system.